Plastic Recycled PP/PE Filler Master Batch Granulating Machine
ATE Twin Screw Extruder adopts modular design principle, component standardization manufacturing, which can present stable and reliable performance.Thanks to the modular principle, ATE extruders can provide highly customizable solutions according to customers' process and special requirements. Based on different output torque grade, ATE series extruders have basic type and efficiency type.
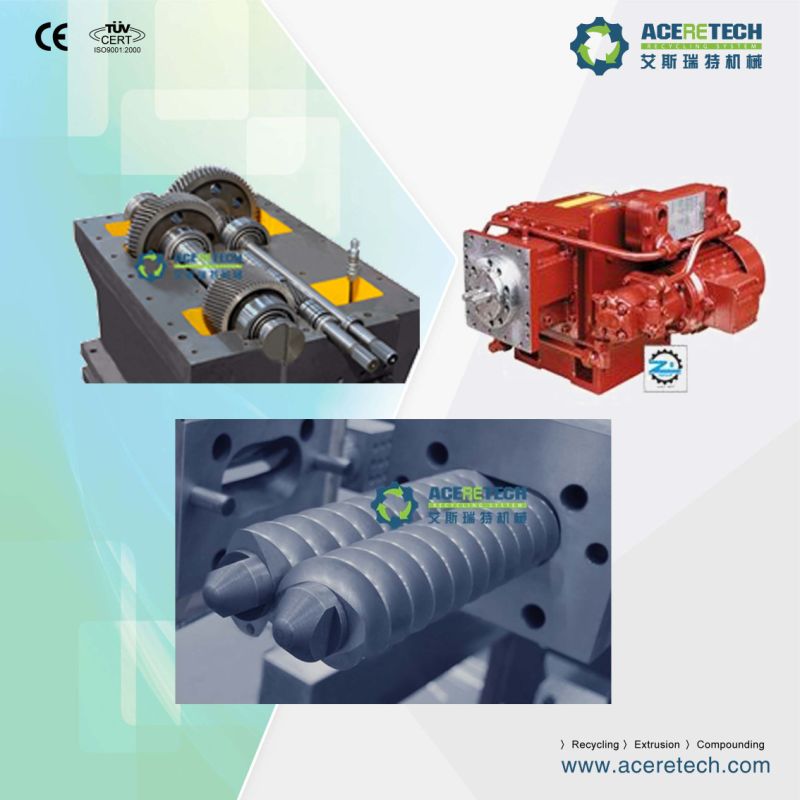
Process section includes barrels, screw shafts, screw elements, individual temperature heating and cooling unit. Barrels and screw elements are designed in block principle.
Block structure allows the screw elements combine and sequence optimized to realize the process:
Conveying-Plasticization- Compounding & Dispersion- Homogenization- Degassing- Pressure building
Also Block structure allows the barrels adjust freely to the fit the process requirement.
Based on different process position, ATE extruders have different barrels type: feeding barrel, side feeding barrel, close barrel, open on top barrel, vacuum vent barrel, etc. According to the different jobs' requirement, barrels' materials can be nitride steel or bimetallic steel.
Multiple cutting system can be combined with ATE Twin Screw Extruder, such as strands pelletizing, hot-face cutting and under-water pelletizing, etc.
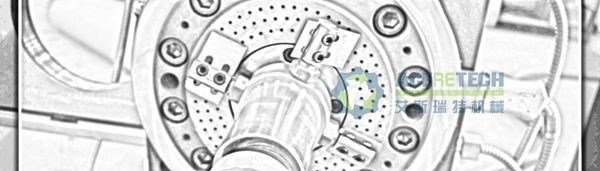
Both Instrument control and PLC control are available to apply in the ATE electrical controlling system. All the key electrical parts adopt European brands to guarantee the controlling system with significant and stable performance.
Parameters of ATE Twin Screw Extruder:
Machine Size | Screw Diameter(mm) | L/D | Screw Speed Max.(rpm) |
Motor power(Kw) | Torque per shaft(Nm) | Specific torque T/A3 |
Throughput rate(kg/h) |
ATE35 | 35.6 | 32-64 | 600 | 15 | 115 | 4.2 | 40-80 |
ATE52 | 51.4 | 32-64 | 600 | 55 | 415 | 5.2 | 150-250 |
ATE65 | 62.4 | 32-64 | 600 | 90 | 675 | 4.8 | 200-400 |
ATE75 | 71 | 32-64 | 600 | 132 | 990 | 4.6 | 300-700 |
ATE95 | 93 | 32-64 | 600 | 315 | 2365 | 5 | 550-1500 |
Typical applications
Engineering plastics |
Masterbatch |
Filling |
TPE/TPR/TRV |
Direct extrusion |
Why choose us
1. Technical documents
All labels on ATE Twin Screw Extruder and lay-out drawings, Electrical diagram, User Manual, will be in English. We should send all necessary files to the buyer since the third week since project execution. All documents in hard copies should be also shipped with machines togetherÂ
2. Arrangement for inspection, installation and testing work
a. After all machines are delivered to customer's factory; Buyer is responsible for all preparation work, e.g. electricity supply, water supply, labors and cranes, etc.
Â
Â
c. The Buyer will buy the round-trip air ticket for Engineer if visa application is approved. The buyer is also responsible to bear expenses generated, e.g. visa formalities, meals, accommodation and allowance of USD100 per day for each engineer.
Âd. Engineer will give free training lessons to labors in buyer's factory.
Â3. Quantity and quality guarantee
a. Quantity/Quality Discrepancy to destination port during transportation:
In case of quality/quantity discrepancy to destination port in transportation, customer should file claim within 30 days after the arrival of the pp pe pellets production system at port of destination. We will be responsible for any discrepancy of the goods caused by shipping company and other transportation organization and/or post office.
Âb. Guarantee period and after-sales services: 12months since installation finished in buyer's factory
During this guarantee period, we will provide spare parts without any charge in case of quality discrepancy caused by us. If the malfunctions are caused by your incorrect operations, we will provide the buyer spare parts at cost price.
Âc. Long-term service:
We will charge the buyer cost price of spare parts beyond one year and provide long-term technical guide
Packaging & Delivery
Packaging Details: | Film and wood as internation sea shippment standard for whole pp pe plastic pellets production system |
Delivery Detail: | 60 working days before delivery |
Â
In the decoration, or in the production of furniture, we need to use a variety of adhesives, and there are many products for bonding, hot melt adhesive is a more commonly used one.
1. Introduction
The Hot Melt Adhesive For Furniture is a kind of adhesive specially used for artificial plate paste, which is an environmentally friendly and solvent-free thermoplastic adhesive. When the hot melt adhesive is heated to a certain temperature, it is transformed from a solid state to a molten state, and when it is coated to the surface of the wood-based panel substrate or edge sealing material, it is cooled into a solid state, and the material and the substrate are bonded together.
2. Ingredients
The basic resin of hot melt adhesive is the copolymerization of ethylene and vinyl acetate under high temperature and pressure, that is, EVA resin. This resin is the main component of the production of hot melt adhesive, and the proportion and quality of the basic resin determine the basic properties of hot melt adhesive.
3. Application
More and more varieties of hot melt adhesive, more and more widely used, can be bonded leather, glass, metal, wood, luggage plastic, medical, textiles, etc., but mainly used in packaging corrugated paper and thick cartons, books wireless binding and woodworking welt.
Hot Melt Adhesive For Sofa,Strong Adhesive Hot Melt,Sofa Mattress Hot Melt Adhesive,Sofa And Mattress Hot Melt Adhesive
Shenzhen Tongde New Materials Technology Co., Ltd. , https://www.tdhotmeltglue.com