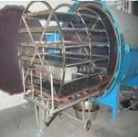
1. The short process time saves energy. Compared with the traditional steamer, the energy saving is up to 80%.
2. The quality is stable, the precise control of temperature and humidity can be treated equally in every production batch.
3. The investment recovery period is short, which is lower than the investment cost of imported equipment, and it is significantly more energy-efficient than domestic equipment.
4. No impact treatment, no condensation spots.
5. Both temperature and humidity can be adjusted.
6. Suitable for handling the loading of yarns in trolleys and yarn carriers.
7. Can handle a variety of natural and synthetic fiber yarns, blended yarns.
Second, the low elasticity of the heat setting 1. Typical steaming process steps vacuum - preheat - humidification - insulation. Constant temperature - vacuum cooling - end 2. Unique preheating system During the process of steaming, the water spot on the sewing thread is a common problem. The water spot can cause dyeing and other problems in the downstream process. Therefore, the steaming preheating process is absolutely necessary, especially It is wool yarn.
3. The heat setting of low elasticity yarns in each production process (spinning, twisting, weaving...) will cause a tension effect on the yarns and fibers, and the effect of tension will cause the yarns to become tangled. Tension and tangling can cause problems in the downstream process. The stress relaxation of the molecular structure in the man-made fiber causes the fiber to shrink. Therefore, Junda's Low Elasticity Setting Machine has brought yarn and silk yarn production. best choice. Studies have shown that the following types of yarns must be steamed for relaxation and shaping: low elastic yarn, cotton yarn, wool yarn, polyester/cotton blended yarn, polyester yarn, core-spun yarn (spandex), sewing thread, artificial fiber yarn, acrylic Tow, mesh knitted fabric (crimped fibers). Saturated steam is the ideal heat-setting medium. It easily permeates into the interior of the package and releases energy during condensation. When the yarn is heated to a specified temperature, its temperature deviation is maintained in a very small range.
Third, the humidification of low elasticity In the production process of the low elasticity, the moisture of the fiber is continuously volatilized. From the raw material to the bobbin, the cumulative humidity decreases by more than 4%. Therefore, the humidification of the low elasticity yarn has become an important part of the contemporary textile process. As a component, it can compensate for the loss of low elasticity and improve the quality of the low elasticity. Different spinners have different low elasticity index, and increasing the speed of the machine will result in a large loss of weight (moisture). The high temperature and friction inside the machine will evaporate the moisture in the low elastane and reduce the quality of the low elastane, which is not conducive to the subsequent processing steps. The humidification treatment can solve this problem. In addition, knitting and weaving can also benefit from the humidifying process (steaming) before the sewing thread is used. Proper packaging of low elasticity yarns in transport, such as in-line bag or yarn tray tension-wrapped packages, can maintain the moisture of the low elasticity yarn. The study on the weaving process shows that the low elastane yarn is better than the non-humidified one (dry yarn) after being humidified. When the weft woven fabric is made of a humidified sewing thread, the number of stops of the cloth machine is greatly reduced. In addition, the strength and elongation at break of the low-elastic filaments were improved, the hairiness was reduced, the weaving efficiency was increased by 2%, and the flying dust was also significantly reduced in knitting. In trade, the buyer never accepts additional markups, and the increase in sewing thread weight is an increase in profits. In general, the payback period for the low-elasticity humidification equipment is less than one year, and the payback period for the low-elasticity humidification equipment is even less than six months. In addition, the quality requirements of export trade also need to continuously improve the quality of low elasticity yarns. Therefore, the humidification of low elastane has become an important part of the textile process.
Fourth, the treatment effect 1. Relax, shape, humidify.
2. Increase sewing thread strength, reduce breakage (cotton yarn breaking strength will increase by 10%, wool yarn breaking elongation increase by 30%).
3. The hairiness of cotton yarns is reduced by 30-45%.
4. The sewing thread has a uniform humidity, and the precision of the controlled moisture regain is high.
5. Eliminate static electricity and improve the yarn unwinding effect.
6. Soft feel.
7. Improve the color effect.
8. Improve production efficiency and improve product quality.
Fifth, the benefits of the following process 1. Knit 1.(1) Low tension yarn with unwinding tension and efficiency up to 20%;
(2) Soft yarns reduce needle wear;
(3) From the beginning to the roll forming, always maintain a balanced and optimal friction value;
(4) In the knitting process, the coil is formed evenly;
(5) The size of the finished product is stable;
(6) No additional humidification system required;
(7) Eliminate static electricity.
2. Woven (1) yarn breakage reduced by 15%;
(2) Reduce 30-45% of lint and fiber fly, improve quality;
(3) Improve yarn strength and improve weaving efficiency;
(4) The fabric is softer.
3. Twisting/warping conditioning and conditioning are done in a single process.
Junda Machinery not only provides you with advanced and ideal styling equipment, but also provides you with various types of setting solutions such as yarn setting, printing and color fixing, curtain shaping, sock shaping, vacuum shaping of socks, stereotyped garments, and yarn resurgence.
Four Wheel Trolley,4 Wheel Hand Trolley,4 Wheeled Shopping Trolley,4 Wheel Trolley Cart
Dalian CS Logistics Technology Co., Ltd , https://www.dlcsems.com