Due to the increasing shortage of raw materials worldwide and the growing demand for environmentally friendly energy production, the development of the solar cell industry is growing rapidly. If such batteries have so far been mainly produced by manual or semi-automated production, then with the continuous advancement of robot technology, more and more automated production will be realized in the future.
In Germany alone, which is the world's largest and fastest growing market due to high funding costs, a total of 1.5 GW of photovoltaic solar cells can be produced annually (in 2007). To date, the production capacity of various solar cell production equipment is only 15 to 20 MW. Equipment with a capacity of 100 to 150 MW has been designed and has been successfully built. The investment required for these equipments is 350 million euros. In a few years, equipment with a capacity of 1.2 GW will be built, and this power jump is impossible without automation.
Establish a new field of solar technology
Kuka Systems of Augsburg is aware of this situation and has been involved in the new business of solar technology since June 2006. Based on extensive automation experience in the automotive industry, the goal has been to make greater achievements through comprehensive automation in order to significantly reduce product costs. If the production cost of solar cells in 2004 was 4 euros/W, it can now be reduced to less than 1.5 euros, and in 2010 it is very likely to drop significantly below 1 euro/W (about 0.7 euro/W).
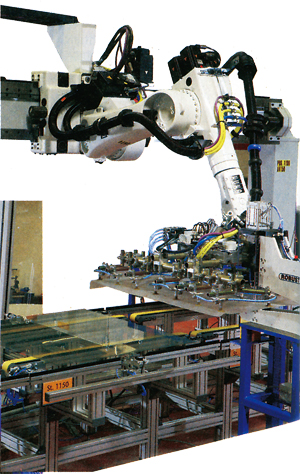
Figure 2 The robot places the film on the glass with the corresponding gripper
Kuka Systems is a complete supplier in this field, providing turnkey services based on customer needs and operating independently. The quotations mainly include design and engineering, project management and quality management, equipment manufacturing, as well as robot battery, equipment and equipment, as well as after-sales service and maintenance. Figures 1 and 2 show the robot is doing power testing and the robot uses the corresponding gripper to place the film on the glass.
Kuka Systems offers module automation manufacturers a single automation solution, such as robot-based solar cell blocks, which include operations such as glass, film lamination, quality inspection, lateral brazing or external frames, as well as complete sets. Automation equipment. In the silicon module technology, including dicing, film-to-module; in thin layer technology, from pressurization to smearing, modules.
Well-known and complex robotic processing islands in automobile manufacturing, also known as robotic parks, are also suitable for the solar cell industry. The solar cell robot production line can even manufacture large solar cell modules including electrical connections within 10s. Even at extremely high speeds, such a set of equipment can reliably and accurately move 10t glass in 1h. If you consider that each glass plate is thin and quite sensitive, then this is a huge job.
Optimize the manufacturing process
Engineers are not only planning to provide more automation, but also to optimize the manufacturing process itself. In a new external frame solution, the aluminum frame needs to be mounted on the solar cell module by robots, and this technology has been implemented twice. Another challenge is the robotic tape, which automatically and accurately attaches the tape to the battery module.
First of all, due to the comprehensive experience in automobile manufacturing, the company has achieved a good reputation in welding, pasting, sealing, assembly and testing. In the first full solar business year, it achieved 3000 in solar technology in 2007. Thousand euros of sales. Kuka Systems expects sales to reach 100 million euros in 2008. Moreover, this new business area has made this robot manufacturer a big step in not relying solely on the automotive manufacturing business.
Excellent results
Elisabeth Schärtl, director of solar technology projects, has been involved since the beginning, emphasizing the high demands and highlighting the quality, speed and precision of equipment and machines. Mr. Albert Vontz, Product Manager, supplemented his statement and emphasized: “In solar cell manufacturing, only with high precision can the battery module have a high efficiency of continuous operation for more than 20 years.†3)
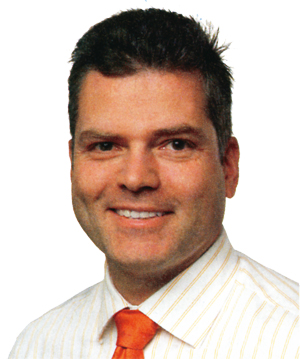
Figure 3 Mr. Albert Vontz, Head of Solar Products at Kuka Systems, said: “There is only a high degree of precision in the manufacture of solar cells to ensure long-lasting efficiency.â€
How serious is Kuka Systems' business of solar technology? How successful has it been? To date, orders for production equipment with a total annual production capacity of 450 MW are evidenced. Together with Spire of the United States, in 2007 a set of automatic production equipment with an annual power of 100 MW was launched. In addition, Kuka Systems has partnered with the most famous manufacturers in Europe, such as Schott Solar, Oerlikon Solar and CIS-Solartechnik.
New technology emerges
It is particularly worth mentioning that the CIS-CIS solar technology, which has just emerged, uses the chemical elements copper (Cu), indium (In) and selenium (Se). If this Bremerhavener company breaks through, solar technology can revolutionize. Based on the above chemical elements, CIS has developed thin-film solar cells that require less semiconductor materials and energy than silicon. In the end, not only the manufacturing cost is greatly reduced, but also the environmental benefits of the CIS solar cell can be greatly improved compared with the current products. The company's manufacturing process uses a non-vacuum method that uses simpler techniques and uses a flexible metal film as the carrier material. This will be an ideal prerequisite for a simple and fast sizing process for new solar cells.
The functional layers of the CIS solar cell are placed layer by layer on the carrier tape. In the current demonstration line, the carrier strip has a width of about 4 cm and a maximum length of about 2000 m which is wound on a reel. The carrier is continuously coated until it is finished into a finished solar strip.
The electroplating method used has a high throughput of materials for manufacturing semiconductors, and this method does not require an ultra-cleaning workshop environment. Other processes, such as the process of making back contacts and window layers, are currently not technically capable of replicating using a non-vacuum process, so these aspects still use conventional jetting techniques. In the future, these aspects will also adopt a lower cost alternative.
After the coating process, the solar strip is assembled with a surface Grid to form solar cells of different sizes (width 4 cm, length 5 to 60 cm) and different powers.
At the end of 2009, 30 MW of production equipment will be built, which is surely responsible for the necessary automation engineering by Kuka.
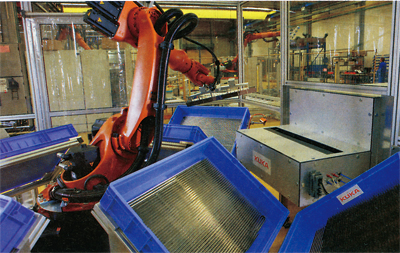
Figure 1 The robot is doing a power test: the solar module is divided into the corresponding boxes by the measured energy power.
Ningbo Xuanchang Electric Co.,Ltd. , https://www.xuanchangpurifier.com