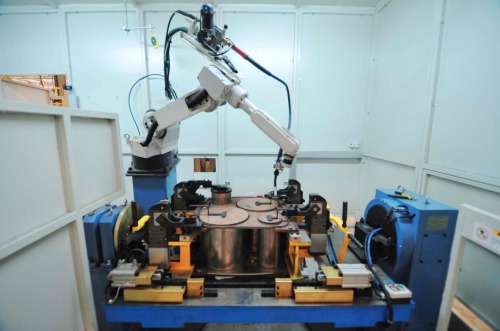
Since the beginning of the special project, it has given great support to the manufacturing equipment in the automotive field. This is because more than 50% of the output of the high-end CNC machine tool industry serves the automotive industry. Therefore, if it can achieve a breakthrough in the automotive field, it will upgrade the machine tool industry. Significant.
In 2012, the economic indicators such as sales revenue, commodity output, and industrial added value of Jinan No.2 Machine Tool Group achieved a positive growth in the context of an average decline of 10% in the machine tool industry. Even more exciting is that the company is at the high end of the world. The market has made major breakthroughs.
On December 20, 2012, the launching ceremony of two fully automatic twin-arm high-speed stamping line projects for Changan Ford Motor's new construction plant in Hangzhou was held at Jinan No.2 Machine Tool Group Co., Ltd. This is the third time after the United States KCAP (Kansas) and DSP9 (Detroit) two production bases, Ford bought the second stamping equipment (including nine large multi-link presses). This event was also a typical example of the success of the machine tool companies in successfully entering the international market. It was selected as the top ten news for the China Machine Tool Industry Association in 2012.
It is reported that this is the world's highest level of complete set of stamping equipment orders won by Jiji Machine Tool and other world-class companies such as Germany. It is also the first time that Ford has purchased non-German production stamping equipment in North America for the past 20 years. A new record for single export orders for Chinese machine tool companies. The Ford project was hailed by the relevant leaders as the most important achievement since the implementation of the “04 Special Projectâ€.
In fact, with the implementation of “04 Special Project†as the turning point, Jinan No. 2 Machine Tool has been adhering to technological innovation in recent years. Since 2009, the company has invested 570 million yuan in its own funds, and has concentrated on the implementation of “enhancing the manufacturing capabilities of large CNC machine toolsâ€. "Developing automation for stamping equipment," "CNC machine tool castings and machining," and "upgrading heat treatment capacity and technological transformation," and other major investment projects.
In fact, the Jinan No. 2 machine tool is only a microcosm. As of the end of 2012, a total of 90 projects in the machine tool industry passed acceptance.
The China Machine Tool & Tool Association once conducted a survey at an exhibition. 69.4% of people thought that “04 Special Project†played a big role, and 26.9% believed that the role was general.
Among them, those who hoped that "acceptance measures should be more rigorous" reached 38.0%, ranking first in the survey. This shows that the respondents pay more attention to the implementation of special projects. In addition, respondents who believe that the “report procedure should be simplified†amounted to 29.8%, and 28.7% said that “the reported information should be more openâ€.
This shows that the vast majority of people recognize the industry transformation and upgrading of “04 Special Projectâ€, but the implementation process is also of great concern to the industry. More people hope that the relevant national departments will be more open and transparent in the process and disclosure of information when they approve special projects. More detailed acceptance criteria.
At the end of last year, at the end of last year’s “China Automotive Equipment Manufacturing Innovation Alliance Directors Extending Meeting,†Fu Yuwu, Executive Vice Chairman of the China Automotive Engineering Society, said that in the past ten years, China has become the world’s largest producer and seller, and the industry has a high degree of optimism. In 2020, it will be referred to as an industrial power.
“Now it seems that the road to a powerful automobile industry is much more difficult than expected. There is no possibility of cornering and overtaking, and there is no situation where we are in the first tier.†Fu Yuwu said that the reason is that he did not master the core technology. , And the picture frame is even more serious than ours, and there is a big gap with foreign technology. Among the key technologies in the automotive industry that are more prominent are vehicle development and database, industrialization of automatic transmissions, automotive electronics, and automotive light. Quantum, smart car and new energy vehicle battery technology.
These need the exploration of the automotive industry companies, but also need the co-creation of the automobile manufacturing equipment industry. To solve these problems, it is necessary to establish an innovation system that integrates production, education, and research with the theme of the enterprise. Through alliances, large-scale cross-industry and inter-disciplinary platforms will be combined to promote the common development of the automobile manufacturing equipment industry and the automotive industry.
He believes that “04 special item†is an opportunity for industrial cooperation. Can it thoroughly sort out the needs of enterprises on the basis of investigations, determine the specific equipment required by the auto industry, and promote the convergence of production, research, and research on the platform of cross-border alliance to form a small loop? To promote cross-industry and interdisciplinary cooperation.
Wang Decheng, deputy head of the “04 special†overall group and vice president of the Machinery Science Research Institute, said that since 2009, there has been great support for manufacturing equipment in the automotive sector, and some projects have achieved important breakthroughs. For example, the stamping production line of Jiji has been exported to Ford of the United States. Some hot-working forming equipments have achieved breakthroughs in stand-alone and common technology, and some complete sets of equipment have also been made.
However, the manufacturing equipment in the automotive field needs to withstand the test of high product productivity and long production cycle of customers, and meet the high requirements of customers for the accuracy and reliability of the equipment. If only one or two or even dozens of prototypes come out, it is far from being able to solve the problem of equipment in the automotive field. Therefore, Wang Decheng believes that from a special point of view, it is difficult for the project of automobile manufacturing equipment to tackle problems, and the challenges are great and the pressure is also great.
"But this is also the driving force for the special work of auto equipment manufacturing during the 12th Five-Year Plan period."
Wang Decheng, the promotion result, said that the problems of automobile manufacturing equipment cannot be solved exclusively, but the special needs of the industry can be put forward through special projects and solved through multiple ways. More importantly, after receiving special support, we must pay attention to the promotion of results and industrialize achievements or form standards, in order to truly solve key technical problems in some industries through the implementation of special projects, and form a group of reliable and well-received users. Manufacturing Equipment.
At the meeting, the experts of the expert group unanimously agreed that in 2014, the automobile manufacturing equipment special project needs to determine the key direction by condensing the most important needs of the industry or upgrading the past achievements.
For example, the development of intelligent manufacturing equipment is the focus of support in 2012, including intelligent manufacturing system integration and demonstration applications, and the development and innovation of core intelligent measurement and control devices. Its supporting direction is industrial robots, robot-based automotive welding automation production lines, and automotive and mechanical processing. Safe experiment system, efficient intelligent die casting island and flexible automation equipment production line.
In the future, it will continue to support the automotive manufacturing equipment field, such as mechanical processing digital workshops, intelligent welding workshops, high-precision forging digital workshops, tire forming digital workshops, flexible automated assembly workshops, industrial robots and key components.
"These projects are the goals of the next phase of the machine tool industry." Wang Decheng stressed that "04 Special Projects" are getting higher and higher in the project's new technologies and processes, making it more and more difficult to declare and requiring high acceptance. Enterprises in the application for "04 special" need to pay attention to, in the scope of key tasks, to have scale and technology, to implement the user, for smart special projects, through the alliance, to obtain two project support.
Wu Bulin, executive vice chairman of the China Machine Tool & Tooling Industry Association, once said that the current market demand, industrial base, and policy environment are conducive to the upgrade and development of the machine tool industry in view of the transformation and upgrading of the entire equipment industry. In recent years, the domestic market share of CNC machine tools is about 60%, and about 40% still rely on imports. This is also the most favorable condition for us to develop medium-to-high-end machine tools, and it is also the most solid foundation for industrial upgrading.
From the perspective of the policy environment, on the one hand, “04 Special Project†will be implemented until 2020. It will be able to concentrate some funds to focus on solving some key issues that need to be resolved urgently. On the other hand, it will be the five key areas in high-end equipment manufacturing as a strategic emerging industry. One of the directions is intelligent manufacturing. CNC machine tools are one of the key points. The mainframes, numerical control systems, and functional components of CNC machines are all listed as key support directions.
However, it is not time for me to wait. The significant changes in the current market demand environment have brought business difficulties to the industry. How to change is what each company must think about. From another perspective, however, it provides an opportunity and an entry point for the transformation and upgrading of the industry. The formed force mechanism provides a powerful impetus for the transformation and upgrading of the industry.
Tungsten carbide roller has characteristics of good wear resistance, high temperature red hardness, thermal fatigue resistance and thermal conductivity and high strength , have been widely used in high-speed wire rod, bar, rebar, seamless steel tubes, etc. Domestic production of tungsten carbide roller materials mostly WC- Co, WC- Co- Ni- Cr two series, and the content of Co, Co- Ni - Cr is in the range of 6wt% ~ 30wt%. From the use of perspective, tungsten carbide rollers has good mechanical properties, its flexural strength up to 2200 MPa or more, shock toughness up (4 ~ 6) × 10^6 J/ m^2, Rockwell hardness (HRA) is up to 78 to 90, widely in the high-speed wire rod rolling process, which is much higher than single-slot chilled cast steel or high speed steel rolls.Tungsten carbide is made of Tungsten Carbide Powder and binder phase (such as drilling, nickel, etc.), and then pressing and sintering, regardless of the conditions under cold rolled or hot rolled has excellent wear resistance, tungsten carbide rollers has been widely used in pre-finishing mill and finishing of high-speed wire rod currently. On the performance of tungsten carbide roller in hot-rolling wire rod , the material must meet the following requirements:
1. Sufficient anti-fracture strength;
2. Good abrasion resistance;
3. The smooth surface finish;
4. Excellent corrosion resistance, thermal fatigue, thermal cracking performance.
Tungsten carbide roller rings can working in bad conditions , small profile rolling (especially rebar rolling) process conditions is harsher than the high-speed wire rod, and therefore corresponds to the profile rolling ,tungsten carbide rollers recommend using high binder phase carbide.
Tungsten carbide roller material design
Pre-finishing all vehicles roller should ensure its high toughness, strength, rigidity and thermal conductivity, followed before considering its wear resistance. When designing each vehicles roller, pre-finishing materials should choose carbide grades of Co, Co- Ni- Cr binder content is high (greater than or equal to 25wt%) , requiring an average WC grain size of coarse (5μm ~ 6μm), to obtain a higher shock toughness, proper strength and hardness. For the finishing of the roller movements, particularly the last two rollers of the finish rolling, which suffered load is small, and high relative velocity of the material to be pressed (80 m / min ~ 120 m / min). In this case, the wear resistance of the roller to be the most important requirements, and must ensure the strength , timpact toughness and hardness of a reasonable match, so the binder of Co / Ni content ratio and the average grain WC control of particle size and other factors must have greater control in front of different pre-finishing rolling roll.
Tungsten carbide roller category
According to the structure of tungsten carbide rollers, it can be divided into solid tungsten carbide roller and composite tungsten carbide roller. Solid tungsten carbide rollers have been widely used in pre-finishing and finishing stands high speed wire rod mill (including fixed reducing the rack, pinch roller rack). Composite tungsten carbide roller is made of cemented carbide and other materials, and it can be divided into tungsten carbide composite roll rings and solid tungsten carbide composite roller. Tungsten carbide composite roll rings mounted on the roller shaft; solid tungsten carbide composite roller will be directly cast in the roll axis to form a whole, a large load is applied to the rolling mill.
Tungsten carbide roller production process control
Tungsten carbide rollers produced by powder metallurgy method, the key to its process control is the chemical composition of the material and the mixture was prepared, pressed molding, sintering and deep processing and other preparation process parameters.
1. Preparation of starting material (WC focus quality): As the WC raw material and quality control of the use of different levels of quality may fluctuate, resulting in adverse effects on microstructure.
2. Preparation of the mixture: Mixture preparation is the key to the production process of the roller, the roller of failure modes - trachoma, mainly generated by this procedure.
3. Pressing: roller pressing is an important process of the roller mill.
4. Sintering: roller sintering is to determine the final quality of the roller production processes, use of advanced low-pressure sintering technology, HIP sintering technology can greatly improve the performance of roller.
5. Deep processing: deep processing rollers have a greater impact on the quality and accuracy of the roller surface.
Carbide Roller,Carbide Ring,Mill of Rolling Line,Steel Wire Rod,Mill Rolling Finish Stand,Mill Roller Groove Type
Luoyang Golden Egret Geotools Co., Ltd , https://www.hvofpowders.com