Domestic use of floating or flotation has long been used, and the actual use of electricity in production is after 1964. Under the conditions at that time, the electric sorting machine developed had only one Φ120 × 1500mm double-roller electric sorter, and this equipment was still used more frequently. Due to the influence of historical conditions, the efficiency of electro-selection is very low, and the process is complicated. The final concentrate quality and recovery rate are not ideal. In particular, only the coarser grains (greater than 60-100 mesh) of white tungsten can be sorted. Tin sill, but less than this size can not enter the electrification, and the return amount of the mine is very large.
The actual process of electrification of scheelite in a mine in Hunan is introduced. The plant uses a Φ120 × 1500mm double-roller electric separator (voltage 17.5kV), the flow of which is shown in Figure 1.
The raw material is the mixed coarse concentrate after re-election, and the sulfide ore is removed by lifting and floating, and then electrified after drying. When the material enters the power contained in the mineral is selected from: 70% scheelite, cassiterite about 15 to 20% hematite and limonite about 5%, bismuthinite 2%, 1% molybdenite about. In addition, there are a small amount of zircon, pyrite, sphalerite, fluorite, wolframite, bismuth and the like foam. Due to the desulfurization by the stage, the raw materials contain sulfur, phosphorus , arsenic and copper .
Figure 1 Flow chart of electrification of scheelite in a mine in Hunan
The process test shows that the recovery rate of white tungsten is only about 60%, and the grade is as high as 74.51%, but the tin content in the white tungsten concentrate is often more than 0.2~0.3%, rarely less than 0.2%; the electrification of cassiterite can not be obtained. The concentrate must be subjected to secondary magnetic separation and re-election (magnetic separation to wolframite and other magnetic minerals), and the final tin concentrate has a grade of only 47.3% (Sn), and the recovery rate is about 90%, but contains WO. 3 is more than 20%, which is an unqualified concentrate.
For the white tungsten and cassiterite of the above mines, a large number of tests were carried out using DXJ type Φ320 × 900mm high-voltage electric separator. When the materials less than 1mm were electrified, the electro-election process was greatly simplified, only one time. Select high-quality scheelite concentrate, WO 3 ≥70% in scheelite concentrate, recovery rate of 90~95%, tin (Sn) less than 0.2%; -0.42+0.1mm The grain size is only one time. The WO 4 is 70.4%, the (Sn) is 0.14~0.18%, the ε WO3 is 96%, the cassiterite recovery rate is 96~97%, and the cassiterite grade is once. The selection can reach more than 40%. If the tin concentrate is selected once, the grade can reach more than 50%, and the recovery rate is 96%.
A selected factory in Guangdong also uses the above Φ120 × 1500mm double-roller electric separator. The raw materials come from the black and white tungsten coarse concentrate of each mine. The same is pre-screened into various levels, and then the black tungsten concentrate is separated by dry strong magnetic separation, and the remainder is white tungsten, cassiterite, sulfide ore, mica , apatite and quartz . The particles are floated to the sulfide ore, and then the white tungsten and the cassiterite are enriched by a shaker, and the obtained concentrate is dried and then electrified. The difference is that the material is divided into narrower grain sizes: -2+1.4, -1.4+0.83, -0.83+0.2 and -0.2mm. Each particle fraction enters the electrification separately, and the electro-optic process is generally the same as that of a certain mine in Hunan (five times of electrification), and finally the total scheelite concentrate contains WO 3 >65% and Sn is 0.2-0.3%. ε WO3 ≥ 80%.
Now the plant does not need Φ120 × 1500mm double-roller electric separator, and after using 60kV high-voltage electric separator, the amount of white tungsten concentrate is increased by about 20%, tin concentrate production is increased by 22%, and tin recovery rate is increased by 9.55%. It can be seen that the use of high-voltage electrification is more effective than the low-voltage electrification in the past.
Japan's Otani Mountain Concentrator, which treats coarse concentrates 60t per month, also uses electro-selection to sort scheelite and cassiterite. The raw material contains sulfide ore and is first removed by flotation. The equipment used is an electric separator with Φ125 × 500 and Φ125 × 1000mm and a voltage of 20kV. The raw materials are narrowly classified into individual particle sizes such as +10, -10+20, -20+40, -40+80, -80+150 mesh (or 180 mesh). The magnetic minerals are first removed by magnetic separation, and then electrified several times. Only the recovery rate of white tungsten was reported to be 95%, no white tungsten grade and its tin content and tin recovery rate and cassiterite grade were observed.
In addition, the Soviet Union has conducted a lot of research on stellite cassiterite containing various minerals in raw materials. The main raw material of cassiterite (Sn 9.7%) and scheelite (WO 3 7.9%), followed by titanium, iron, monazite, quartz, and the like. The particle size is 0.1~0.6mm, and the process flow combining electric and magnetic separation is adopted. After multiple sorting, the results are shown in Table 1.
product name | Yield,% | Product composition, % | Recovery rate,% | ||
锡石 | White tungsten | 锡石 | White tungsten | ||
Concentrate (conductor) Middle mine Tailings (non-conductor) Feed mine | 53.3 14.6 32.1 100.0 | 90.9 35.7 0.2 59.4 | 0.6 11.3 11.3 17.7 | 92.1 7.8 0.1 100.0 | 1.9 10.1 88.0 100.0 |
From the above results, the effect is not outstanding, and the finest grade can only reach 150 or 180 mesh. In addition, electrification can also be used for the selective separation of black and white tungsten ore.
EVA Traction Pad is the tail pad to be sticked on the surfboard. It comes with center arch and kick tail, which allow surfers to control the direction and stability when surfing in the sea.
The design of surfboard traction pad can be in one piece, two pieces, or three pieces basically. The standard the classical texture for traction pad would be diamond like texture, as it can provide the stronger grip among all of them.
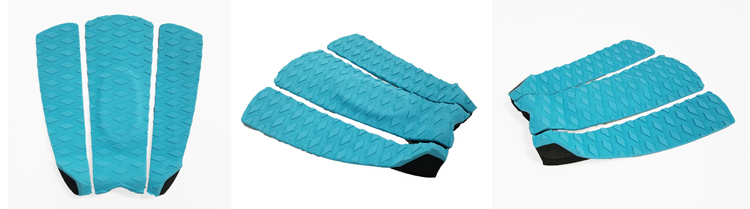
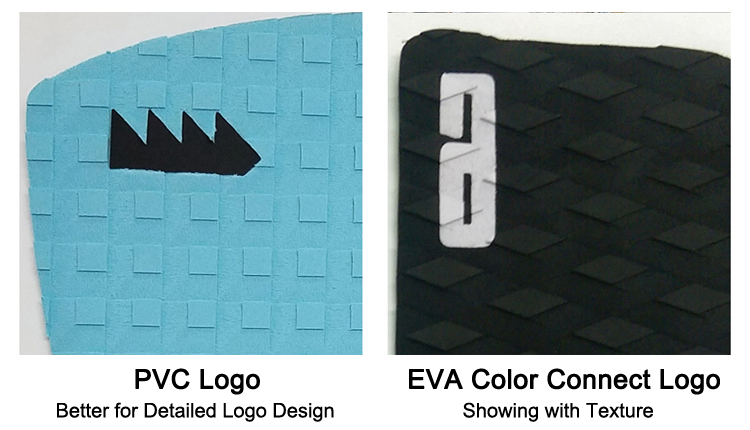
The EVA color connect logo is made along with the pad itself. Unlike the PVC logo, it is also EVA material same as pad, and also shows with the texture. The design of this logo can not be too detailed and small, it needs to be larger and simpler so that we can use the different color EVA material to connect them.
Eva Traction Pad,Non-Skip Traction Pad,Traction Pad,Surfboard Tail Pads,Grip Tail Pad,Eva Tail Pad
Huizhou City Melors Plastic Products Co., Limited , https://www.foamexpert.net