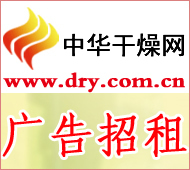
China's first alkaline compressor anti-fouling agent product has revived the first domestic styrene device that has been in existence for more than 50 years. The reporter learned last week from PetroChina Lanzhou Petrochemical Company that the company's annual output of 60,000 tons of styrene equipment uses domestic compressor anti-fouling agent to replace imported products for 6 months. Under the same injection volume, the compressor exports and exhaust gas The inlet polymer of the condenser was significantly reduced, the corrosion point of the ethylbenzene vapor evaporator did not occur, and the corrosion of the dehydrogenation unit equipment was effectively controlled. The old petrochemical plant also achieved the effect of energy saving and long-term stable operation after adopting the new alkaline compressor scale inhibitor.
This new type of oil-soluble alkaline compressor scale inhibitor is a new product independently developed and produced by Beijing Spiral Technology Development Co., Ltd. This product is a structural component of alkaline products developed specifically for the weak acid medium process of styrene plants and has now been granted a national invention patent. The product not only effectively prevents self-agglomeration of active olefins such as styrene at high temperatures, but also does not require heating when used in a low-temperature environment.
The result of industrial application for more than six months shows that the domestic new alkaline compressor scale inhibitor has achieved the effect of “one stone with two birdsâ€: In the case of domestic compressor compressor with the same injection amount as the imported product, the compressor-controlled outlet polymerization of the compressor The amount of material is reduced by 42.5%, the polymer at the inlet of the exhaust gas condenser is reduced by 32.2%, and the corrosion of the dehydrogenation unit equipment is also effectively controlled.
It is understood that the styrene tail gas compressor is the key core equipment for the styrene plant. The first is to provide sufficient negative pressure for the ethylene dehydrogenation reactor, and the second is to recover the styrene in the tail gas to increase the production efficiency of the plant. However, the styrene compounds in the exhaust gas are prone to polymerization fouling, resulting in a drop in compressor operating efficiency, resulting in reduced load on the entire styrene plant and even forced shutdown. This has become a major bottleneck affecting the long-term stable operation of styrene equipment. The most effective way to solve this problem is to inject anti-fouling agents into the compressor and the exhaust gas condenser.
According to reports, Lanzhou Petrochemical's 60,000-ton/year styrene plant was the first styrene plant in China built and put into operation in 1960. In 2004, it reached an annual production capacity of 60,000 tons. The plant has long used exhaust gas produced by US companies. Compressor scale inhibitor imported products. Since the imported compressor antiscalant products are water-soluble additives, not only is it difficult to raise in winter, but also steam heating of the filling system of the entire device is required, which not only increases the cost and energy consumption of the device, but also increases the number of workers. The intensity of labor operation. In April 2012, Lanzhou Petrochemical Company decided to use domestic new oil-soluble alkaline compressor scale inhibitors in styrene plants.
Rubber Oil Seal,PTFE O Rings,Silicone O Rings
Yuyao City Xinxing Plastic Moulds Co.,Ltd. , http://www.fittingmold.com