ä¸‰ç§ Metallurgical Rolling Production Process The three types of coal waste heat resources are used for comprehensive heat generation for power generation. The waste heat system must satisfy the energy balance of the main metallurgical production process, and must also meet the energy balance of the heat production process of the waste heat gas. The study of energy balance and control principle of process power generation has great social significance for the comprehensive environmental protection, waste heat utilization, energy optimization, and economic benefits of the metallurgical industry. 
I. Analysis of Energy Balance System and Controllable Boundary The production process of the metallurgical industry is a large-scale continuous production process. There are many uncertainties in the generation of blast furnace, coke oven and converter gas. No matter the gas type, gas volume, or calorific value will change with the production process. The demand for electrical and thermal loads in captive power plants also varies with the metallurgical production process. Relying on the operator's operation and control, there is no time to follow the flow of the gas types, pressure, flow, heat value fluctuations and changes in the load of a variety of variables in real time.
 The production process is a very complex multivariable object, and this huge energy balance system is automatically deployed to automatically maintain the input and output energy balance of the entire energy system. No mature and simple control method can directly resolve the balance of this system. . 

For example, if a blast furnace is stopped, metallurgical gas in the process flow will be significantly reduced, the reduced gas volume will exceed the boiler load adjustable range, and at the same time there will not be enough supplements for coke-oven gas and converter gas, we must consider stopping one. Taiwan boiler. The load on the electric heating load point is reduced and a steam turbine is stopped.
Maximize the use of waste heat, maximize the use of gas resources to generate electricity and heat, and prioritize internal power and heat load requirements of the company. When defining the automatic control plan, we must first determine the control boundaries of each process section on the gas, power generation and demand side. The analysis is as follows:
 1) The change of the operation mode of the metallurgical production process: The change of the operating mode of the main flow is a prior variable, and the operation mode of the power plant must be adjusted through the dispatching instructions.
2) Input and withdrawal of large equipment at the demand-side load point: According to the technological production needs, the increase or decrease of electricity and heat equipment will affect the output of the power and heat load of the power plant, and also adjust the plant through dispatching instructions. Operation mode.
 3) Failure of the main process: Since there is a gas storage tank, it will not affect the fuel bed supply of the power plant in the first time. After the failure information, the power plant must have corresponding fault protection measures. The dispatch center shall promptly issue instructions based on recoverable faults or non-recoverable faults to guide and adjust the production and operation modes of the power plant.
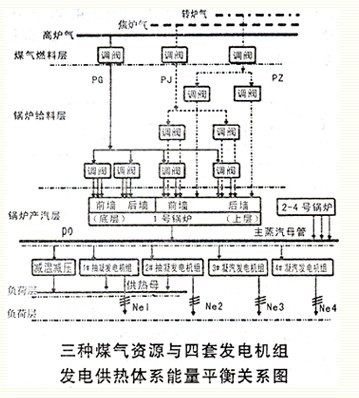
4) Retreat or failure of power generation equipment: The startup, shutdown and operation of the boiler steam turbine equipment in the power plant are based on the value command.
As shown in the figure above, according to the energy balance relationship of the total system, in order to facilitate the energy balance adjustment control of each segment, we divide this large system into four relatively independent and correlated sub-energy balance systems.
The production of the three kinds of coal gas in the plutonium process is balanced with the boiler fuel consumption in the power plant, and all the gas is sent to the boiler;
å…¥ The fuel of the four gas-fired boilers will be balanced with the steam energy sent to the parent pipe to ensure that the pressure of the parent pipe is stable;
 The steam energy of the mother pipe is balanced with the electric load of each electric load point, and the internal load has priority;
 The steam energy of the mother pipe is balanced with the heat load of the heating network, maintaining the pressure of the heating network and not affecting the power supply;
In order to maintain the balance of the major thermal systems of the main process gas and power plants, within the adjustable range of the thermal system, the principle of regulation of the thermal system balance level of each sub-section is:
 1) Using gas to set steam: Maximize the use of the combustible gas produced by the steelmaking furnace, and convert all generated gas into a boiler and turn it into steam;
 2) Complementary gas volume and content: The production of the three types of coal gas and the calorific value of the three types of gas are all changed within a certain range, and the three types of gas can automatically produce “gasâ€. That is, if the CO content of a gas is measured to be low, the shortage of the gas flow compensation content is automatically increased, or the additional heating value is automatically followed up through two other gas routes. Make sure to enter the total heat of the boiler.
 Total output heat = boiler efficiency x input total heat  3) Steam: The steam generated by the boiler is to be used to maximize power generation. Power generation prioritizes the balancing of internal electrical loads, insufficient power or excess balance on the grid. The condensing unit is dedicated to generating electricity. The steam extraction unit selects "electric heating" to prioritize electric loads while maintaining heating.
4) Heat set by heat and heat by electricity: The steam extraction machine can be operated by "heating with electricity or heating with electricity", and selecting "heating with electricity" to provide heat load as the main factor, adjusting the adjustment of the steam turbine. The pressure regulator changes the thermal load provided while providing the electrical load. Extraction units can also be "heated by electricity," depending on which load is more important to the process and more back-up support system support.
 5) Heat supply network balance: Within the adjustable range of the unit's extraction steam load, the unit's pressure regulator regulates the heating load to ensure the heat network pressure is stable. Exceeding the adjustable pressure range of the unit, it is necessary to rely on the desuperheater and pressure reducer to regulate the heat load. Or rely on other steam sources to ensure.
 To realize the automatic control of large thermal systems, according to the control domain of conventional PID control laws in DCS, it is necessary to carry out thermodynamic balance control of one circuit at the level of expert solution. The optimal distribution of the load, including the optimal allocation of gas resources, cannot rely on a control loop, and complete the entire control from the change of gas resources to the load on the Internet through one instruction. Sometimes, the thermodynamic system overcomes external and internal small disturbances with balanced input and output, and has self-balancing capability. The introduction of DCS control will enable the system to obtain timely and accurate balance effects no matter when small disturbances or large disturbances occur.
 In the semi-thermal or cold state of the power generation equipment, the boiler steam turbine cannot be automatically put into operation. At this time, the main process of the gas surplus is to use reserve or short-term venting. The coordination of the main production methods of steel plants requires the dispatch center to optimize. In emergency situations, it is more important to maintain safe production than waste heat utilization.
In short, special conditions cannot be included in the scope of automatic regulation. Only under the premise that the relative balance of large thermal systems is determined, that is, the main process will generate approximately XXX kcal of gas, with XXX electric load and heat load demand. Put in X-boiler and start X turbine. Within a certain range, through DCS to achieve optimal distribution of gas load, automatic adjustment of electricity, heat load.
Second, the principle of two-fuel gas fuel optimization optimization  three combustible gas: metallurgical gas, converter gas and coke oven gas. The lowest calorific value of metallurgical gas and the highest calorific value of coke oven gas. The gas with low calorific value has a low ignition temperature and is easily turned off, which is not conducive to stable combustion. The higher the boiler's load during combustion, the more stable the combustion; the lower the load, the less stable the combustion.
 First allocation: The fuel distribution is to prevent the boiler from low load extinguishment and ensure that each boiler operates at more than 50% load. The first time the fuel is distributed, it must initially meet the gas fuel source that maintains more than 50% of the load of each boiler. The boiler 50% load calorific value is provided by the thermal calculation of the boiler plant.
Total heat formula: R(aG×COG×QG)+(aJ×COJ×QJ)+(az×COz×QJ)
R——Total calorific value of three kinds of gas mother pipes;
aG——average conversion coefficient of CO content and calorific value;
COG - real-time CO content of metallurgical gas;
QG - real-time flow of boiler gas;
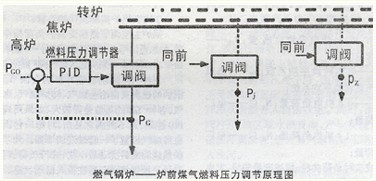
The energy dispatch center will release the total amount of all kinds of gas, use the CO content of all kinds of gas mother pipes, calculate automatically and add them, divide the heat consumption of a boiler by 50% of the rated load (see boiler plant thermal calculation), and decide to invest Several boilers participated in the operation and regulation. The total amount of the three kinds of coal gas is commanded by the dispatching center, and the operation mode of the power plant is determined by the value. The DCS can automatically perform the first allocation calculation based on the three total gas measurements.
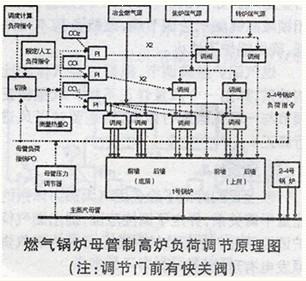
Second distribution: According to the principle of "gasification with gas": To maximize the use of various gas resources generated by the process, we only maintain the pressure of the gas ahead of the furnace slightly higher than the furnace pressure, and maximize the gas produced into the boiler. Using the pressure of each gas precursor gas pipe PG/PJ/PZ as a control quantity, set three gas pipe pressure control loops, maintain the PG point pressure setting slightly higher than the pot pressure, so as to ensure that the gas entering the furnace is half the value of the flow The source, regardless of the amount of gas that the boilers consume, can reliably and stably stabilize the gas fuel in front of the furnace, as long as the distribution is reasonable. Once the PG point pressure has changed, the gas pressure regulator automatically adjusts the opening of the regulating gate to maintain the pressure at the PG point. This is called the second allocation of fuel. 
Since the number of boilers put into operation was determined in advance, in order to prevent a certain boiler from contriving for gas sources, the same gas pressure settings in front of several furnaces must be consistent, and the second fuel distribution task can be completed automatically and accurately. The second distribution is very important for stable combustion of the boiler. 
PG01=PG02=PG04
PJ01=PJ02PJ03=PJ04
Pz01=Pz02Pz03=Pz04
 DCS can automatically measure the total heat of the three kinds of gas, and the electric load measurement parameters of the load point, using the thermal calculation formula, unified conversion into heat to calculate. DCS completes real calculation and input and output energy balance control. 
ΔN1# furnace = (R-(aeNe total + aR total N total) / 4 
N# steam condenser = Rpo/4-aeNe1
△N#1 Extraction Machine=Rpo/4(aeNe1+aRNR1)
In the formula: R--the total heat of the gas mother tube; Rpo-the total heat value of the steam mother tube;
ae——Electrothermal conversion average coefficient; aR—The average system of hot steam and coal gas heat conversion;
Ne1——1# electromechanical load capacity; Ne total—the total electric power plant load;
NR1——heat load of No. 1 machine; NR total - total heat load of power plant;
Generate real-time load curves, increase and decrease output curve, power generation curve, and heat supply curve.
Third, the gas boiler control principle
The constant steam-pipe pressure is a sign of the balance between boiler steam supply and turbine steam consumption. During operation, the steam mother tube pressure is kept constant. The four boilers operated by the parental control in parallel must respond to changes in the pressure of the parent pipe to maintain the stability of the parent pipe pressure. If one boiler is not responsible for the variable load operation, two boilers can be used, and the other boilers can be operated with fixed loads. 
The measured heat signal of the boiler is used as the main control of the fuel, and the amount of change of the gas mother COG is taken as the feedforward correction amount. The amount of air distribution, and the amount of fuel through a small value comparison selector, take the smaller one as a given value of the fuel master, in order to ensure that the dynamic process, the amount of fuel is less than the amount of air. 
IV. Main points of gas boiler combustion master control
Although the gas flow rate can be measured, the calorific value component of the gas is changed within a certain range, and it cannot accurately reflect the actual fuel quantity signal of the boiler. The heat signal Q is used instead of the gas quantity signal to adapt to changes in the gas composition. 
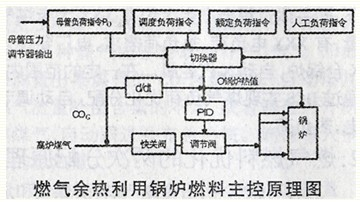
Q=D+CdPb/dt
In the style: D is the boiler steam flow. 
C is the heat storage capacity of the boiler. 
Pb is the drum pressure. 
Q represents the actual heat load of the boiler. 
After the boiler master regulator receives the boiler load command signal, it compares with the heat signal Q and sends a fuel opening command. The opening command determines the opening of each gas valve.
差异 The difference in the combustion of three gases will affect the quality. The boiler fuel comes from metallurgical gas, converter gas and coke oven gas. The calorific value of various gases varies greatly. If the same PID control is used, the quality cannot be satisfied. Each boiler has a set of combustion regulators for each type of gas. In order to minimize the disturbance of the boiler's natural burning, only one type of gas regulator is put into automatic state when carrying out load adjustment. 
If the boiler output reaches the upper limit, then the lock pressure will increase the gas total control valve, and the other three furnaces will allocate excess metallurgical gas. If the boiler load is <50%, an alarm will be issued. At this time, the total reducing valve of the boiler gas will be blocked and the load will no longer be reduced, ensuring that the boiler does not stall. 
Gas boiler air supply regulation, according to the proportion of three kinds of gas, calculate an air volume correction factor. The adjustment of oxygen content and the adjustment of carbon monoxide are fine adjustments, both of which are required to correct the supply air. 
V. Concluding remarks
Above, we discussed the energy balance of large-scale heating system of metallurgical gas, defined the scope of regulation, and put forward the principle of gas boiler regulation. It is hoped that there will be theoretical implications for the original generation of gas from the metallurgical industry. 
Food Hygiene Inspection Laboratory
The environment of the food testing laboratory should be kept clean, dust-free, odorless, noiseless, and suitable for temperature and humidity. The decoration design should consider facilities such as air purification, ventilation, lighting, water and electricity to ensure that the environment inside the laboratory meets standards.
Jilin HaoChen cleaning Engineering Technology Co., Ltd. is a technological innovation enterprise focusing on the pharmaceutical purification engineering industry. The enterprise has a superb purification engineering technical team and excellent construction force. The company has always pursued the service tenet of "safety first, quality-oriented, customer first and technology first". Many representative air purification projects have been established in Jilin Province, Heilongjiang Province, Liaoning Province and Inner Mongolia Autonomous Region. With a registered capital of 5.8 million yuan, the company has grade II qualification for professional contracting of Building Decoration Engineering; Grade II qualification for professional contracting of building electromechanical installation engineering.
Service Items:
Purification project of pharmaceutical clean workshop (pharmaceutical purification workshop, food purification workshop, electronic and chemical purification workshop, etc.)
Construction of purification operating room (hybrid integrated operating room, DSA operating room, laminar flow purification operating room, ordinary purification operating room, etc.)
Construction of ultra clean laboratory (Microbiology Laboratory, sterility laboratory, PCR laboratory, physical and chemical laboratory, P1, P2, P3 laboratory, etc.)
Construction of SPF animal feeding room purification project
Business items: medical purification color steel plate, supporting purification profile, air purification ventilation equipment, purification engineering supporting equipment, etc
At present, the company has 8 sets (pieces) of various large and medium-sized mechanical equipment, the original value of mechanical purification equipment is 4.6 million yuan, and the net value of mechanical purification equipment is 2.3 million yuan. The total annual construction output value is about 10 million yuan. Our company has 24 registered employees. Among them, there are 15 personnel with professional titles, 7 engineering technicians, 3 senior engineers, 5 engineers and 7 assistant engineers; 2 persons with economic management titles.
Morality first, customers first, safety first and economy first!
We look forward to working with you.
Food Hygiene Inspection Laboratory,Department Of Health Food Inspection,Industrial Hygiene Laboratories,Food Laboratory And Equipment
Jilin HaoChen cleaning Engineering Technology Co., Ltd , https://www.hccoalgas.com