[ China Instrument Network Instrument Development ] Recently, Siemens researchers have developed a virtual sensor that can calculate the internal temperature of the motor without using a sensor installed inside the motor. The information obtained from this can avoid unnecessary downtime - this improvement will greatly reduce operating costs.
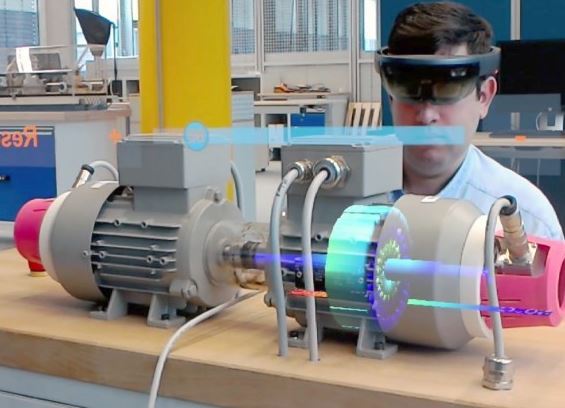
The rotor of a large motor such as a compressed gas, although bulky like a room, is difficult to access. This type of rotor generates high thermal stresses at startup and can cause damage if overheated. Therefore, its temperature must be monitored.
The motors that drive such rotors are so-called salient pole machines, which are commonly used to drive high-power pumps in the oil, gas and chemical industries. Since they are not equipped with a frequency converter and are directly connected to the grid, they generate a lot of heat when starting up. If it is repeatedly started, its internal temperature may rise to 800 °C, which may cause serious damage. For this reason, the motor must be allowed to cool down before restarting. The question is: How long does it take? The temperature in critical areas inside the motor cannot be measured directly. As a result, technicians have so far only been able to estimate the duration of cooling. In general, the expert sets a buffer period to rule out the possibility of damage. This kind of downtime is often as long as 12 hours, which is much longer than the actual cooling time, which causes the operator to suffer huge losses.
By viewing the motor presenter through an augmented reality helmet, the wearer can see the realistic simulation of the motor and its interior, as well as the real presenter superimposed on it.
Virtual sensor
Now, thanks to the work of the Siemens Central Research Institute (CT), researchers can use virtual sensors to measure and monitor the internal temperature of the motor under operating conditions. This development helps to significantly reduce downtime and increase equipment utilization. The mathematical model of the virtual sensor prototype is based on digital twins – it accurately simulates how a real sensor will work if it fits inside the motor. Watching the motor demonstrator through the augmented reality helmet HoloLens, the wearer can see the realistic simulation of the motor and its interior, as well as the real presenter superimposed on it. The different colors from blue to red indicate the temperature level.
Birgit Obst, a simulation specialist at Siemens Academia Sinica, said, “We draw on the work of the Siemens Process Industry and Drives Group, especially from Siemens Siemens Motors in Berlin. They used mathematical models to capture the geometry of the drive when developing the motor. Shape and material properties to create digital twins for each component.†But these models are extremely broad and complex and are often not available for real-time calculations. In the process of solving this challenge, Siemens researchers made two major advances: they successfully applied the mathematical specification method and successfully derived the abstract model. Although these models are not comprehensive, they can still be critical. Simulation results. These models are 1000 times faster than traditional engineering simulation tools, and the precision deviation is smaller and controllable. Thanks to this, Siemens has developed digital twins that can be continuously monitored during operation. These digital twins can provide realistic virtual images at any time. The accuracy of the virtual sensor can be quantified by comparing the data generated by the virtual sensor with the data generated by the sensor on the non-moving component.
Cost savings
Using the new model developed by Siemens researchers, reliable conclusions can be drawn about the rotor temperature of the motor. Dirk Hartmann, coordinator of the core technology of simulation and digital twins at Siemens Academia Sinica, said, “To make a metaphor, this is like a weather forecast. Now we can measure – in other words, calculate – the temperature at a particular location, In this case, that is, the temperature of the rotor. Not only that, but by using the data provided by each measurement point - equivalent to the weather station - we can predict all areas, not just the area being measured."
This ability can save operators a lot of money. Artur Jungiewicz, a developer at Siemens Process Industries and Drives in Berlin, said, “This optimization process prevents the motor from overheating and reduces downtime during the cooling phase, thereby saving up to €210,000 per hour.†A special feature is its speed: the direction of temperature change can now be monitored and predicted in real time.
Demonstration practice
A table-sized demonstrator shows how the Siemens simulation system works: one shaft connects two small motors. The left motor decelerates the right motor and produces a continuous load during this process. The sensor measures the external temperature of the motor. At the same time, data on run time and load can be collected. The simulation system applies these input parameters and the mathematical model of the motor to calculate the internal temperature of the right drive and predict the temperature change.
Hartmann said, “Our virtual sensors are very accurate and measure temperature directly. The prototype measures the current temperature and predicts the point in time when the motor can be restarted in the future.†The basic model from the engineering system “provides valuable The foundation of technical expertise makes our approach different from the completely data-based process that competitors use,†Obst said. Hartmann added, “The engineering model integration chain lays the foundation for online simulation and calibration, which is a unique selling point.â€
(Original title: Siemens researchers have developed a "calculated temperature" virtual sensor)
High Precision Edm Wire Cutting Machine
High Precision Edm Wire Cutting Machine,Edm Wire Cutting Machine,Electrical Discharge Machining,Wire Electrical Discharge Machining
Taizhou Jiangzhou CNC Machine Tool Manufacturing Co.,Ltd , https://www.machinetzjz.com